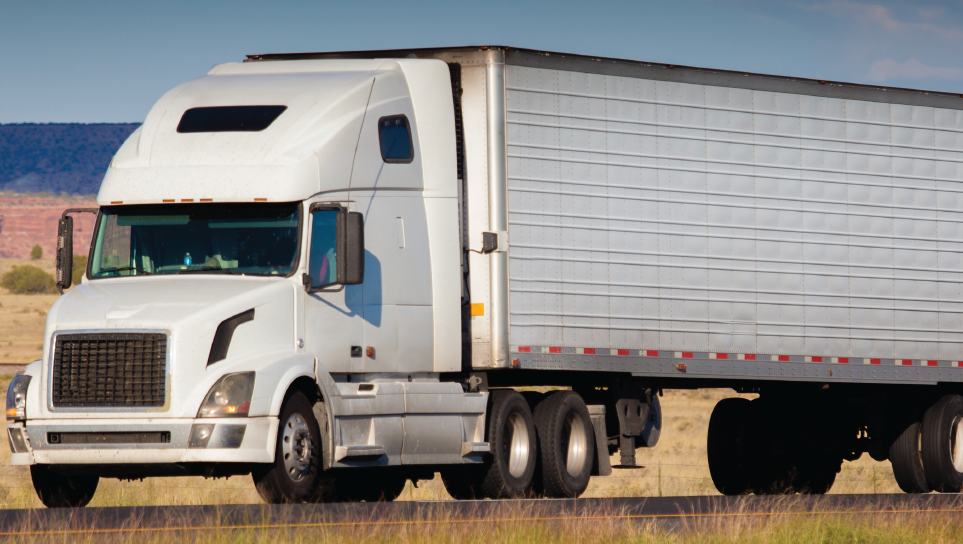
Are you ready to replace your fleet vehicles tomorrow? Are you carefully monitoring your vital components, such as diesel engines, for early, and mostly invisible, warning signs of impending failure?
Contaminants exist in used fluids. However, some are almost always a predecessor to catastrophic failure. To act, you must know they are in suspension. That’s only possible through a managed oil and fluid analysis program. Corrective maintenance is inevitable for anything mechanical. But it’s much more palatable when done early and well before major damage, and downtime, occurs.
Hundreds of thousands of diesel engines breakdown every year due to poor maintenance and oversight practices.
Here’s just two of the most common contaminants:
- Glycol – It is symptomatic of seal failure, damaged cylinder liners and cracked/blown gaskets. Glycol can cause sludge, leading to filter blockage, increase engine wear, cold seizure, increase corrosion and diluted oil viscosity.
- Excessive fuel dilution (greater than 2%) – It is symptomatic of fuel injector problems and improper combustion. Diesel fuel dilution can result in a premature loss of corrosion protection and thickening of engine oil, causing deposits. Fuel dilution can lower the viscosity of a motor oil resulting in premature wear on pistons, rings, liners and crankcase bearings.
Engine failure periods, due to contamination, can vary considerably. Without early detection, they can dramatically shorten engine life by hundreds of thousands of miles. There are no ‘magic elixirs’ available to offset damages caused by these contaminants. Therefore, proactive maintenance and oil analysis are vital to your fleet.