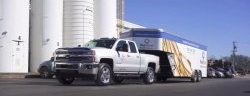
RelaDyne Reliability Services is making an impact on manufacturing. Doug Muennich, RelaDyne Varnish Mitigation Business Development Manager, visited customer, Ventra Plastics, to talk about the impact our varnish mitigation services have had on their operations.
Nestled right off I-75 in Russellville, Kentucky, Ventra Plastics manufactures plastic components for the automotive industry. Their plant was experiencing a lack of productivity and an alarming increase in downtime. According to Chris Sanders, Ventra Plastics Maintenance Manager, “We were changing [pumps] sometimes up to four and five times a week” due to varnish within their systems.
“I was tired of changing pumps, I was tired of going through valves, I was tired of the downtime, I was tired of working 14 – 16 hours a day fighting a losing battle,” described Sanders.
RelaDyne presented our patented varnish mitigation process as the appropriate and effective solution. The patented process is performed while the system is running, meaning no maintenance downtime, an absolute must for most manufacturers.
Doug Muennich, along with the rest of the Reliability Services team, began mitigating varnish one hydraulic system at a time, resulting in increased cycle times, productivity, and decreased downtime.
“When you work with RelaDyne, it’s more like a partnership,” said Chris Sanders.
Call today for a MPC Patch Test and Oil Analysis to see how we can help you return your hydraulic systems to new-like production!
In the meantime, check out the Ventra Plastics case study on our RelaDyne YouTube channel, here.