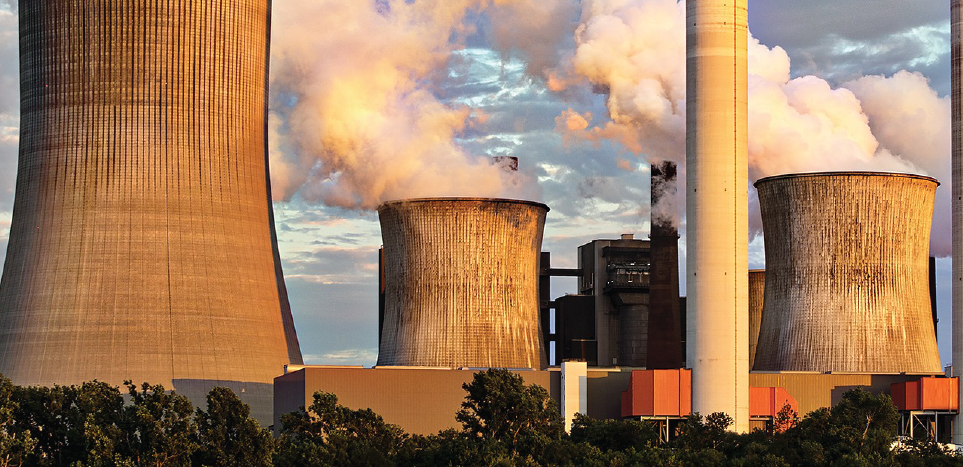
Keeping up with the demands of running a manufacturing facility is daunting. Especially since most manufacturing plants have a 24/7 runtime. There’s not a second in any day that allows for purposeful downtime maintenance. With that in mind, manufacturing plants are forced to keep up with their maintenance during production. What a feat that is! Not only must plants be in tip top shape for general operational needs, but at any time in many manufacturing industries, an inspection can mean the difference between continued production and total consequential shutdown.
Abide by these tips to be inspection ready:
- Ensure all fluids in machinery are tested for contamination periodically and filtered or even replaced as needed.
- An MPC patch test and other fluid analysis can help determined if there is degradation of the oil and contaminants that are affecting your machinery components and can predict decreased component performance or even failure.
- Inspect reduced cycle times and output immediately rather than accepting as the result of machinery lifecycle.
- Though machinery does inevitably age, there are cycle time and output standards that can give insight into what production you should be able to expect from your specific machine. With proper maintenance routines and proactivity in doing so, your machines should be able to keep a like new operating condition for a long time.
- Investigate any uncommon noise or smell that originates from machinery even if machinery is fully operational.
- Unusual sounds or smells during operation can signify a gear, fluid, or other problem that can greatly impact the performance and health of the machine.
Though it can be tedious, following Original Equipment Manufacturers (OEM) processes and maintenance requirements strictly is key to a flawless inspection.