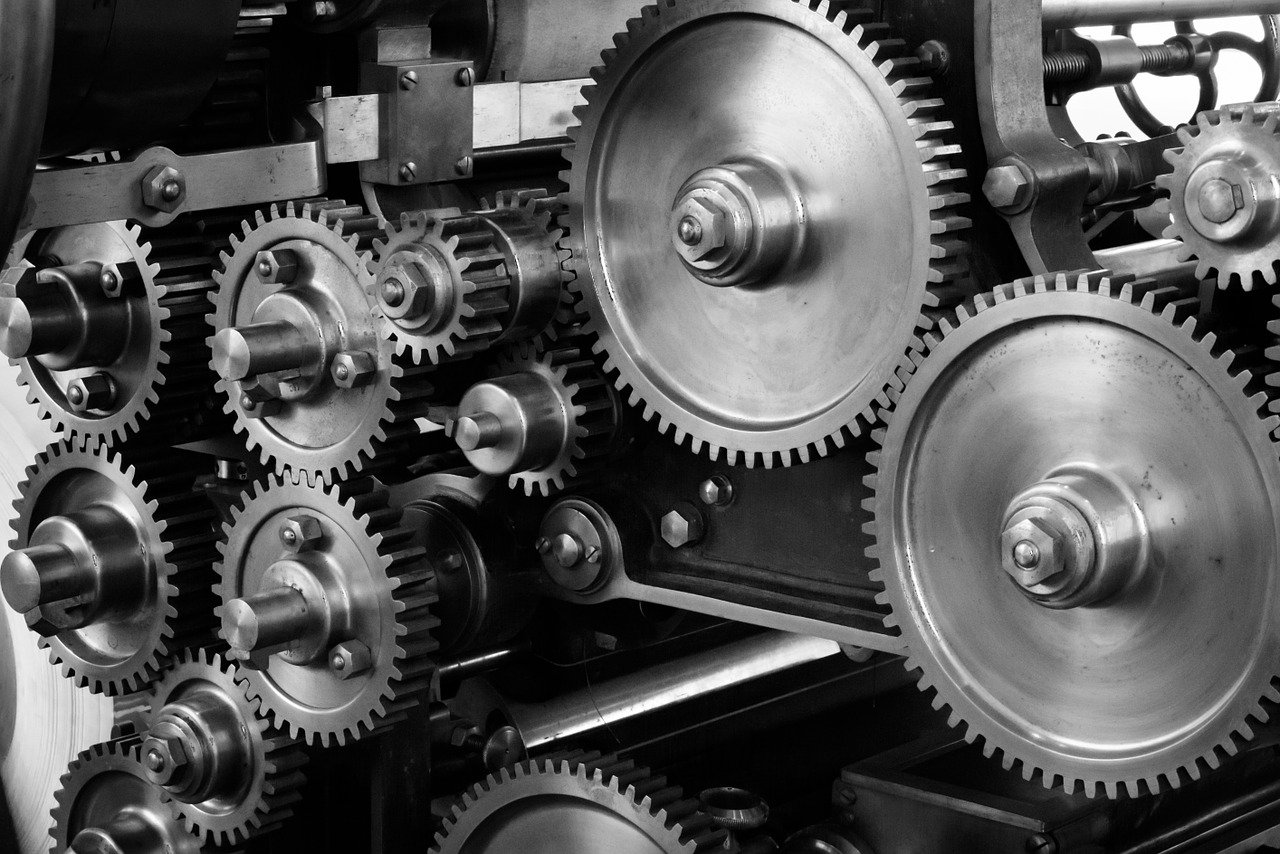
Unexpected shutdowns of any kind are hard to plan for and react to, but shutdowns due to pandemics? For many manufacturers, this became reality in late March 2020. As states begin to reopen, manufacturers are now in the process of restarting production. However, a production restart isn’t like flipping a light switch.
After a careful shutdown of machinery, the restart process is just as meticulous. To protect the machinery and electrical systems that have been idle, it’s important to conduct a comprehensive inspection of all equipment. To ensure a proper restart, make sure to add these three steps to your procedure:
Conduct a fluid analysis on all system fluids.
Idle fluids can wreak havoc on your systems if not properly maintained. Fluid analysis is the best way to check the health of your fluids. This can prevent failure caused by degraded fluids, and help the machinery operate efficiently and productively.
Check metals for corrosion.
While a system is down, corrosion has a unique opportunity to run rampant in equipment that may not have been properly protected prior to shutdown.
Conduct inventory on replacement parts.
As you begin to restart equipment, unexpected component failures can increase your downtime. Prevent prolonging the process of your restart by ensuring all replacement parts are in stock and ready to be installed if needed.
While a comprehensive restart plan includes much more than the previous three steps, these recommendations will make your life easier as you begin production again. In such an unprecedented situation such as a pandemic, the procedures of your facility may need to be totally rewritten to include such circumstances. Patience and a “double-check” attitude will ensure success for your operations.