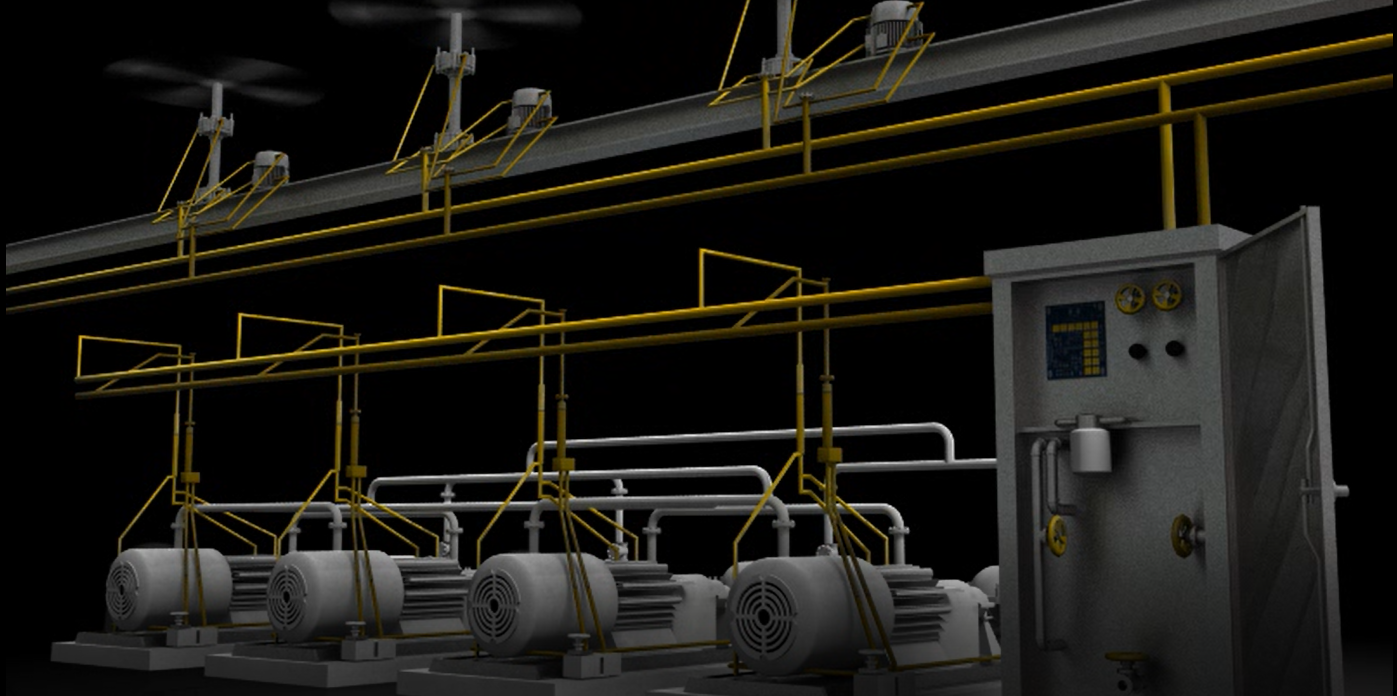
What happens if I lose oil mist lubrication to my equipment?
In most circumstances “probably nothing”. How is that possible? In this article we will explore reasons that may lead to a loss of oil mist lubrication and how bearing lubrication is sustained without a continuous supply of oil mist during an abrupt interruption.
The first thing we need to remember is that the Oil Mist Generator (OMG) is extremely reliable; Heinz Bloch (1) has rated the OMG at 99.99962% reliable. The reason for the high reliability is that the OMG contains no moving parts. The OMG uses the force of air passing over an orifice or through a vortex to pick up oil and break it down into small particles of oil 5 micron or less is size. The compressed air is the only force that transports the oil mist through the system to each individual lubrication point.
If for any reason the flow of oil mist is disrupted or lost, the lubrication will remain with the bearing for extended periods of time, in which this has been proven under supervised and unsupervised conditions. Testing (1) has repeatedly proven rolling element bearings are unimpacted by system failures or interruptions of up to 8 hours duration. There are several questions that are typically asked about oil flow continuity in OMGs.
What happens when there is a loss of electrical power?
Electrical power is not required for the OMG to generate and supply oil mist to the downstream users. It is only required for monitoring purposes and to help optimize the production of oil mist. Even if there is a loss of electrical power, the OMG will still generate and transport oil mist to the required lubrication points throughout the system. If the entire facility loses electrical power than the process unit is coming down and oil mist lubrication should not be of the utmost concern.
What happens when there is a loss of instrument air?
Instrument air is required for the OMG to generate oil mist. If the entire facility loses instrument air than the process unit is coming down and oil mist lubrication should not be of the utmost concern. If the air supply to the OMG is interrupted due to a leak or failed equipment, then it becomes a concern. Recommendations for dealing with the loss of instrument air would be to get the system back in operation before the end of the current shift. Again, do not wait for the next shift to get the system back in operation.
The last factor to stop the production of oil mist would be the loss of oil. The oil mist generator has a maximum oil consumption rate of 2 gal. per 24-hour period of operation. Most misting chambers on large scale systems have a capacity of at least 5-9 gallons, which is sufficient to provide 2 ½ days of operation. Once the low-level alarm istriggered, the unit can still run for 8-12 hours before it is no longer able to produce oil mist. That duration will provide enough of a grace period for the operator to take the necessary corrective actions to remedy the issue. For an oil mist generator to stop producing oil mist due to loss of oil would be due to neglect by either the operator or the maintenance dept.
The recommendation for dealing with the loss of oil mist is to get the system back in operation before the end of the current shift. Do not wait for the next shift to get the system back in operation.
We have 35 plus years of experience on oil mist systems, and we have only seen or heard of few incidents where the oil mist system failed, and all could’ve been avoided if the simple standard operating procedures were implemented and followed. As such, similar to traditional lubrication methods, human error is the primary driver of failure in oil mist systems. These systems require 1/100th the human interaction of tractional lubrication systems, drastically reducing the opportunities for human error.
This is from 35 years of experience with over 2,500 large scale oil mist systems worldwide.
Ref: Update Your Oil Mist Lubrication Knowledge; Bloch, H.P. Hydrocarbon Processing; February 2003.
Interested in learning more? Complete the form, and we’ll be in touch!
Contact Us
Please fill out the form below and RelaDyne will contact you shortly.